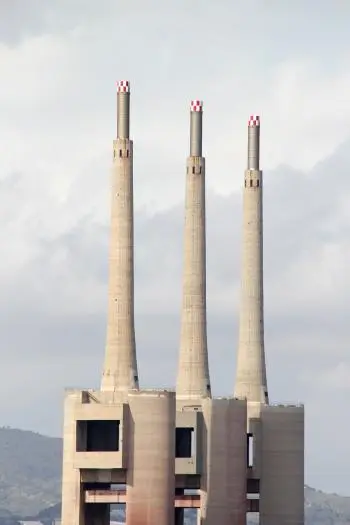
Una central térmica es una planta eléctrica que convierte la energía térmica en energía eléctrica. La diferencia entre un tipo de planta y otro es la forma en que se obtiene el calor.
Las fuentes caloríficas de una central térmica son:
- Combustibles fósiles (carbón, gasoil y gas natural)
- Reacciones nucleares de átomos de uranio.
- Biomassa.
- Energía solar.
Las dos primeras son fuentes de energía no renovables. En cambio, la biomasa y la energía solar se consideran energía renovable a pesar que la primera emite gases de efecto invernadero y las centrales de energía solar térmica no.
¿Cómo funciona una central térmica convencional?
Una central térmica convencional es una planta termoeléctrica que puede utilizar carbón, petróleo o gas natural como combustible. Son las centrales térmicas más utilizadas a pesar del impacto medioambiental y la emisión de dióxido de carbono y otros gases de efecto invernadero que producen.
El funcionamiento del ciclo de las centrales termoeléctricas convencionales es el mismo independientemente de la forma en que se obtiene calor.
La central térmica típica está dividida en varios segmentos: una caldera, una turbina, un alternador y un condensador.
En la caldera se quema el combustible para obtener la energía térmica. Con esta energía se calienta un fluido para obtener vapor de agua. El vapor se utiliza para accionar una turbina de vapor de esta forma, la energía interna del vapor se convierte en energía mecánica.
Finalmente, la turbina de vapor está conectada a un alternador que transforma la energía en electricidad. El vapor resultante pasa por un condensador para volver a empezar el ciclo.
¿Qué son las centrales térmicas de ciclo combinado?
Las centrales térmicas de ciclo combinado son centrales termoeléctricas que combinan las centrales de ciclo convencional con una turbina de gas. El uso combinado de los ciclos de gas y vapor mejora la eficiencia energética y se consiguen rendimientos cercanos al 55%.
El combustible de este tipo de centrales es el gas natural, el gasóleo e incluso el carbón si está preparado de una forma especial.
La característica principal del ciclo de gas es que no hay cambio de fase del fluido. El proceso es el siguiente:
- Compresión del gas.
- Calentamiento del gas.
- Expansión del gas en una turbina de gas. En este caso la turbina va conectada a un generador eléctrico para producir electricidad.
El gas que sale de la turbina de gas todavía está a una temperatura muy elevada por lo que se utiliza para generar vapor y activar un ciclo convencional de forma paralela.
Centrales térmicas que funcionan con energía solar
Las plantas solares pueden funcionar con energía solar. En este caso, se colocan colectores solares en una amplia superficie que son espejos que dirigen la radiación solar a un mismo punto.
La concentración de toda la energía solar en este punto genera temperaturas muy elevadas que se utilizan para generar vapor.
A partir de aquí, el funcionamiento es el mismo que en cualquier central térmica convencional.
Efectos sobre el medio ambiente
Las centrales térmicas que utilizan combustibles fósiles generan dióxido de carbono y otros gases de efecto invernadero. El exceso de gases en la atmósfera son muy perjudiciales porqué favorecen el calentamiento global del planeta.
Actualmente, las plantas termoeléctricas están obligadas a controlar sus emisiones. Esta obligación es particularmente relevante para las grandes centrales eléctricas en las que hay una sección importante para reducir los contaminantes.